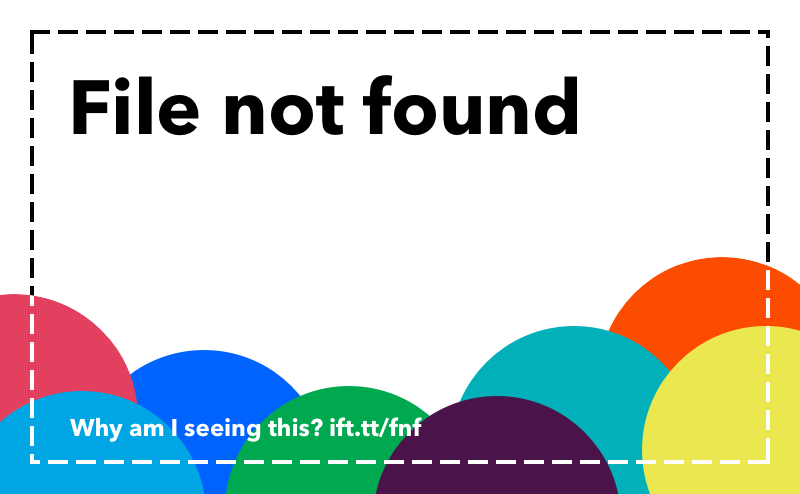
Decided that I needed to create a workspace for me to work on that's not just a plastic folding table in the middle of the garage. I had recently just gotten a bunch of tools and wanted to put them to use to build a spot to organize them as well. This was my first shot at designing something so complex from the ground up and building it all myself. I'd only done very simple projects before, screwing a few 2x4's together and such.Decided to build 20"x48" workbench with a lower shelf and upper shelf that would measure 60" high. Needed to make it exactly 48" wide so that it'd fit in a little nook in my garage between my breaker box and where my stairs jut into the garageHere's a picture of the final product for those who don't like to waitThis was the plan I drew up on my iPad using an Apple Pencil. I initially tried using Sketch Up to make a rendering of the work bench but I couldn't figure it out and gave up. I did a wrong calculation for the top shelf plywood, it should be 10\"x48\" instead of 10\"x45\". Learned a valuable lesson in measuring twice, cutting once.I then used this Google Sheets to estimate what cuts and lengths I needed to cut out of each piece of 2x4, as well as how much plywood wood and how many of what length of screw I would need. I initially forgot to take into account the width of the blade of the miter saw I'd be using to cut the wood, so I had to re-configure the 2x4 cuts to leave at least a few inches extra in each 8 foot 2x4. The only exception were for the 60\" cuts, because those didn't have to be exactly 60\", as long as I had 4 pieces that were about 60\" that were the same length.Here's my initial haul. That's 11x 8 foot pieces of Douglas Fir 2x4's. I needed to have the shop make one cut in each one to fit it in my car, so I looked at my Google Sheets and just picked the longest cut for each 8 foot piece. I also found an old peg board that were exactly the measurements I needed at my mom's house. She used to blow up balloons to stick in the holds so my friends and I could throw darts at them at my birthday parties and stuff. I decided to keep it exactly the way it was with all the old balloon fragments and stuff on it, kind of a nostalgia thing.Here's the pile of 2x4s after I got them cut. I brought everything to my friend's house and used his miter saw to cut everything. I really wanted to make sure each piece was the exact same size as the other pieces of the same size. I know that I am prone to error and can make mistakes measuring by fractions of an inch, so instead of measuring each cut using a measuring tape, I would measure, for example, one 10\" piece, cut it, and then use that piece to measure out cuts for the remaining 5x 10\" pieces. It took a lot of time and patience, but in the end I'm glad I was so careful making sure all the pieces of the same length were EXACTLY the same length.Here is the frame for the work bench table top, which I'll attach a piece of plywood onto to serve as a work surface. First, I laid out all of the pieces to resemble the shape I needed. Then, I used the speed square to make sure every single corner was as square as possible. I marked out where I wanted the size 10 3\" screws to go with a pen, and then clamped everything together so that the frame would at least somewhat hold its shape as I drilled my pilot holes using a 9/64\" bit. Then, I used my impact driver to drill in two screws per connection point, making sure to check the squareness of the corners after I screwed in each screw. This was done very carefully and was very time consuming, but I ended up with a very square frame so it was worth it.I did the exact same drill with the bottom shelf, being very careful to measure the squareness of everything before clamping it and screwing it together. Two 3\" screws per connection point and checking the squareness after every screw. I wanted to make the bottom shelf recessed a little bit compared to the table top so that I could easily sit at the work bench with a stool and store it underneath the table as well. I gave myself about 8\" of space for my legs when I sit and to store a stool. This was the last thing I did on day 1.Start of day 2. After completing the frames for the table top and the bottom shelf, I decided to connect legs to the table top as a next step so that I could have a surface to complete the rest of the cutting and assembly. Here is a leg being attached. Legs were 36\" long. Used a square and clamp to try and get everything as square as possible, same drill as the table top and the bottom shelf with checking the squareness and drilling pilot holes. However, I used 3 screws in the shape of a triangle (think play button orientation) to attach the legs, being careful to avoid the screws that were already in the frame itself. It was very important for me to get the legs as square as possible because I didn't want a wobbly table. Before and after every screw, I checked the squareness of the leg to the floor, leg to the frame, etc.Here's what it looked like after connecting the four legs to the table top. Rock solid and not wobbly at all. See how the legs stick out a bit from the sides of the table top frame? That will play into how I cut the plywood because I wanted the plywood surface to stick out a little bit past the frame to cover the table legs. It also gives me the added advantage of having another surface to clamp onto.I bought 2 sheets of plywood from a lumber shop - 2'x4'x3/4\" for the table top, and 2'x4'x1/2\" for the bottom and top shelves. I used a 50\" saw guide from Harbor Freight to get everything lined up to cut down to size, making sure to leave enough room to cover the table legs sticking out. Basically, I drew a line where I wanted to make the cut, and then measured 4 inches over from that line to place my saw guide. Lining up my circular saw with the saw guide exactly 4 inches over allowed my blade to line up perfectly with my cut line. I was able to use both the saw guide and the drawn line to make my cut as perfectly as I could. Also, I made sure to use my 4 ah battery instead of my 1.5 ah, - I definitely noticed a difference in power.After I cut the plywood for the table top, I used size 9 1 1/2\" screws (the store didn't have 1 5/8\") to attach the plywood to the frame. I used the piece of plywood I had just cut off, measured out even distances between the 4 screws I would use per line, and used a square with the plywood piece to mark out exactly where I wanted each screw to go, making sure each one would go through the plywood and into a 2x4. I used the same 9/64\" drill bit to drill pilot holes before driving in the screws with an impact driver. I found that I broke a couple of the 1 1/2\" screws while driving them, I think I could've gone a little slower to keep the screws from heating up too much. I found they heat up really fast - I burned my arm on one when I rested on it.Now that I had another surface to work on, I decided to put the top shelf together. Here's a better shot of how I clamped the pieces together to make the frame before I started drilling pilot holes and putting the screws in. Again, took my time making sure everything was square before clamping it. Used the same 9/64\" bit for the pilot holes and 3\" screws for the connection points. Two screws per connection point.Did the same drill I did with the table top with the top shelf, connecting four 60\" legs onto the frame by using the square and clamp. Also used three screws per leg to attach them to the frame.After that, I lined up the top shelf with the back of the table top and put the table top in between the top shelf legs. The legs for the top shelf serve as extra support for the back of the work bench. I used two 3\" screws per leg to connect it to the frame of the table top.This is a picture from a little later in the process. I realized that the middle leg of the work bench doesn't really do anything if it extends all the way to the ground and it looks really weird having 6 legs touching the floor, so I used a reciprocating saw to saw it off right past the table top. I used a square to mark off where I was going to make the cut to make sure I didn't cut into the bottom shelf itself when making this cut.Here is the work bench at the end of day 2, sitting in its nook. I didn't take pictures of how I attached the bottom shelf, but I needed my roommate to come down and hold it in place while I attached it to the legs. I used some leftover plywood, measured out 19 inches in length, and then used that plywood to serve as a support for the bottom shelf (along with my roommates' hands) while screwing in the shelf. It actually took quite a bit of wiggling to get the shelf in there to screw in. I probably should have attached it before I attached the top shelf. I made the top shelf 19\" off the ground so I could fit my shop vac under there - you'll see later.Start of day 3, first thing I did was put the pegboard on. I just screwed it in with 1 1/2\" screws into the back of the frame of the whole workbench. I basically used the holes of the pegboard itself to mark out where I wanted the screws to go through to attach to the frame, and then put screws through those holes into the 2x4 beneath. Basically, I used the pegboard holes as pilot holes for the pegboard itself, and didn't have to drill any new holes into the pegboard. I then used an oscillating multi-tool with the plugne blade attachment to cut out the hole in the pegboard for the outlet. I could've done a better job on that. What I did was push the table against the wall and then use a pen to poke the holes in the pegboard to see whether it was outlet or drywall underneath. Then I just cut hole to hole using the multi-tool. I could've done with a slightly smaller hole to fit the size of the outlet better. I also put in a backing board 2x4 at the bottom, figured it'd be good to have a piece like that back there to push things against later. The workbench was like this for about a week while I waited for a few things to arrive from Amazon: a power strip, shop light, and peg board hooks.Got a shop stool from Harbor Freight that fits under the work bench. This picture was after I put in a bunch of the peg board hooks I got. This was a regrettable purchase from Amazon. A lot of the hooks were bent in the wrong way and the plastic bins didn't fit into my pegboard at all. I had to drill holes in them and hang them off of hooks for them to work. I also saw a pegboard hook set at Harbor Freight yesterday for 1/3 of what I paid. Much regret. I cut out some of the 2x4's of the frame of the top shelf to nestle the 30\" LED shop light I bought into it to try and get it out of the way a bit. It didn't really work that well, it was hard to get the hooks just right to attach the light and to get it raised enough into the cut out. I zip-tied a 30\" workshop power strip from Amazon Basics to the pegboard to power everything. Zip-tied the extra power cord down to try and get it out of the way. Bought an air purifier to try and catch as much stray saw dust as possible. Lot of neon green in this picture. Also had a small TV sitting around to decided to put it on the top shelf so I can watch S.W.A.T. while I work. Not quite earthquake-safe but I like having it there.Here's a close-up of the pegboard. You can see the jerry rigged job of attaching the plastic bins on the left. Drilled holes using I think the 9/64\" bit. You can see that the light isn't really recessed into the top shelf very much, wish I did a better job with that to get it more out of the way. The 6 foot cable for the power strip was way too long so I zip-tied it all down to the power strip itself. Also used zip-ties instead of screws to attach it to the pegboard.Here's a close-up of the bottom shelf, where you can see my shop vac just barely fits under. I ran the wires for my battery chargers from the bottom shelf to the top to get them powered. I might consider mounting the chargers somewhere at some point. The recession of the bottom shelf gives me room to sit/stand there and store the workbench underneath.Overall, this project was a blast to make. I'm excited to continue creating in this workspace! via /r/DIY https://ift.tt/3eCgOY1