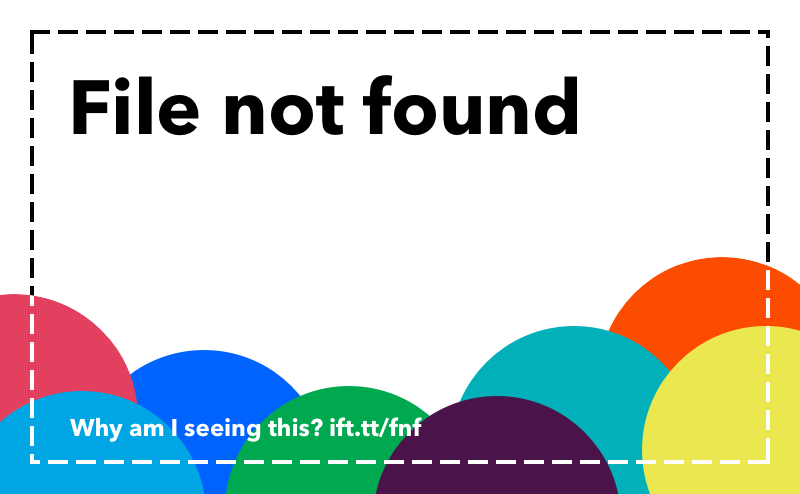
Hi guys. I'm building a robot that is going to have to drill holes in trees. Up until now, we have been using mounted hand drills on the robot connected to a arduino and we didn't do too much programming. However, this method has a lot of problems. Generally, the torque isn't enough. The drills are diagonally aligned as you can see here Imgur and here Imgur. The inner drills don't have enough torque to drill through the trunk of the tree and they just stop at some point. I know that a lot of you have experience with wood, so any kind of advice or feedback on this drilling method is welcome! My professor was convinced we can use a fuel engine and blast torque in the drill, but imo that's way too complex to build because of the complexities of having a reverse when you're done drilling and we would have to build an entire gearbox to run multiple drills.My proposition is to use industrial servo motors as they tend to be a bit more capable than hand drills and can do longer hours without overheating. So I bought this Imgur and I'm trying to figure out the best way to connect a drill bit to this and control the drill. Finally, to prevent the drills from stopping or stuttering I plan to program a control system where the RPM should remain constant by regulating torque.So I want to ask you guys for your insight as I am tasked with redesigning the current model and improving it with the electrical solution. How can I best use this servo to drill holes (This one has enough torque to use three drills at the same time). Any other tips and feedback is welcome! via /r/DIY http://ift.tt/2hdp1Hg